Achieving Excellence in Aluminum Casting: Expert Tips and Techniques
Mastering Aluminum Spreading: a Deep Study the Different Methods Offered
Aluminum casting stands as a keystone of contemporary production processes, providing flexibility and precision in producing detailed designs and practical components. As industries progressively transform to light weight aluminum for its lightweight yet durable properties, understanding the different casting methods ends up being vital. From the conventional method of sand spreading to the complex procedures of investment spreading and pass away spreading, each method presents unique obstacles and advantages. Understanding the nuances of these methods is important for guaranteeing the top quality and efficiency of the casting procedure. In this exploration of aluminum spreading strategies, we will lose light on the details of each method, supplying understandings that could transform your method to light weight aluminum casting.
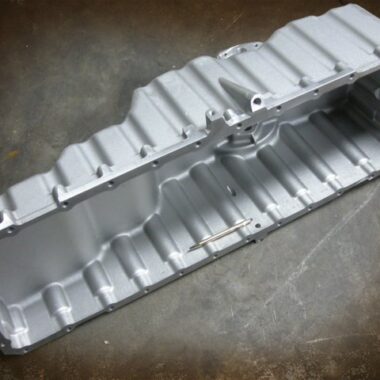
Sand Spreading Technique Review
The Sand Spreading method's convenience and extensive application make it a foundation in mastering light weight aluminum spreading processes. This technique entails developing a mold from a mixture of sand and a binder, such as clay, to create elaborate shapes for casting liquified aluminum. Sand spreading is a prominent selection because of its relatively affordable, convenience of adjustment, and capacity to create complex geometries with high accuracy.
The procedure begins with the production of a pattern, typically made from wood or metal, which is pressed into the sand to develop a mold dental caries. As soon as the pattern is gotten rid of, the mold tooth cavity is loaded with liquified aluminum, which strengthens to take the shape of the pattern. After cooling down and solidification, the sand mold is broken away, exposing the light weight aluminum casting.
Sand casting is extensively used in different industries, including vehicle, aerospace, and production, due to its adaptability in producing both large and tiny aluminum elements (aluminum casting). Its adaptability to detailed layouts and cost-effectiveness make it a recommended choice for lots of light weight aluminum spreading applications
Irreversible Mold Spreading Refine Discussed
Checking out the intricacies of light weight aluminum spreading, the Irreversible Mold and mildew Casting process provides a refined technique for developing premium parts with accuracy and efficiency. Unlike sand casting, long-term mold casting makes use of a reusable mold normally constructed from steel or iron to form the liquified aluminum. The mold is preheated to a particular temperature to improve the flowability of the steel before putting. This process assists achieve a smoother surface area coating and tighter resistances contrasted to sand spreading.
Long-term mold and mildew spreading can be classified into 2 major types: gravity casting and low-pressure casting. Gravity spreading includes putting the liquified steel into the mold and mildew using gravity, while low-pressure spreading utilizes low stress to fill the mold and mildew tooth cavity. Both techniques offer benefits in terms of decreasing porosity and enhancing mechanical properties.
Pass Away Casting: Benefits and Drawbacks
Mastering the complexities of die spreading involves understanding its unique advantages and drawbacks in the realm of aluminum component manufacturing. Pass away casting deals numerous advantages that make it a prominent selection for producing aluminum components. One crucial advantage is the high-speed production ability of die casting, permitting for the mass manufacturing of complex forms with limited resistances. In addition, pass away casting provides superb dimensional precision and smooth surface coatings, reducing the demand for added machining processes. The procedure is likewise very repeatable, ensuring constant top quality throughout big manufacturing runs.
Nonetheless, die spreading does include its very own set of drawbacks. One significant drawback is the high preliminary tooling price connected with producing the passes away made use of in the procedure (aluminum casting). These molds can be costly to create, making pass away casting much less economical for little production runs. Moreover, the procedure is not as versatile when it involves design changes contrasted to other casting methods like sand spreading. In spite of these limitations, the benefits of die casting often exceed the disadvantages, making it a favored choice for lots of aluminum casting applications.
Financial Investment Casting Applications and Benefits
Building on the benefits of die spreading, investment casting offers a functional method for producing intricate light weight aluminum elements with distinct benefits in various applications. Financial investment casting, also recognized as lost-wax casting, succeeds in developing complicated shapes that would certainly be difficult or tough to attain via various other approaches. This strategy is widely used in industries such as aerospace, automobile, and fashion jewelry production.
One of the crucial benefits of investment casting is its capacity to create near-net form components, minimizing the demand for extra machining and decreasing product waste. This causes price savings and faster production times compared to traditional machining procedures. In addition, investment spreading allows for the production of components with outstanding surface coatings and tight resistances.
In the aerospace industry, financial investment spreading is preferred for its ability to produce light-weight yet solid components essential for aircraft efficiency. The automobile market take advantage of investment casting for producing components with high dimensional accuracy and elaborate designs. Overall, financial investment casting uses a economical and exact option for making detailed light weight aluminum components throughout numerous industries.
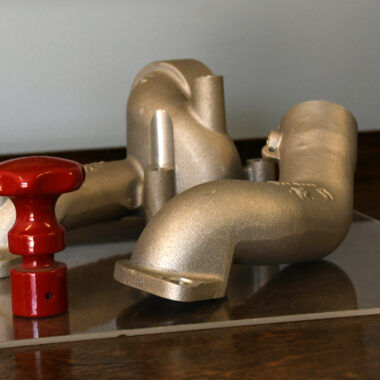
Lost Foam Casting: Just How It Functions
Lost foam casting, additionally called evaporative-pattern casting, is a method for producing elaborate steel components by using foam patterns that evaporate throughout the casting procedure. This technique begins with a foam pattern of the desired part being positioned into unbonded sand. The foam pattern is typically coated with a refractory material to boost the surface finish of the last metal part. When liquified metal is poured right into the mold, the foam vaporizes due to the warmth, leaving behind a cavity that is after that filled by the metal.
One of the crucial benefits of lost foam spreading is its capacity to produce complex forms with elaborate information that might be testing to attain with other casting techniques. In addition, the procedure can be cost-effective as it click this gets rid of the requirement for cores and enables the loan consolidation of multiple components into a single component. Nonetheless, it calls for cautious control of the procedure parameters to make certain proper foam evaporation and metal flow.
Final Thought
To conclude, grasping aluminum casting entails understanding and utilizing numerous strategies such as sand casting, long-term mold spreading, pass away casting, financial investment spreading, and lost foam spreading. Each technique has its very own benefits and applications in the manufacturing procedure. By familiarizing oneself with these various methods, manufacturers can choose one of the most suitable casting strategy for their certain needs and demands, eventually resulting in effective and effective manufacturing over at this website of light weight aluminum components.
From the standard method of sand casting to the complex procedures of investment casting and die spreading, each strategy presents distinct difficulties and benefits. In this expedition of light weight aluminum spreading techniques, we will certainly lose light on the intricacies of each approach, offering understandings that can revolutionize your approach to light weight aluminum spreading.
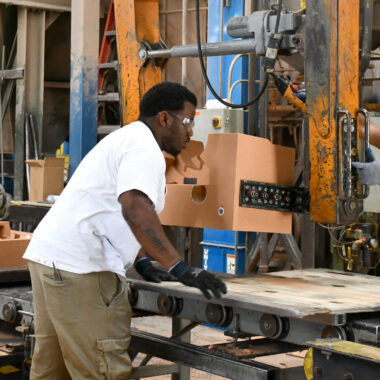